How do Food Co Packers Price for my Food Product?
Costing effectiveness is the primary concern for any existing business.
A Food co packer generally with- stands with multiple organizational dealings which helps them to sustain in the market with strength. Besides it they work on win-win existence with the parent organizations .
Regulations on Costing of Food products
- Per day Output
- Per piece production
Costing Generally done by Co-packers are on the Following Frames
Per Day Output
- Depending on the outcome the co-packer can really provide for you on the basis of your need, the cost effectiveness depends, say, if the plant production quantity is 12 tons per day ,and your need is 20 tons, it generally have to run with another 8 units costing calculations, hence it is recommendable to work with survey of third parties before running on projects.
- It is a general trend for all the organizations to work with bulk orders which helps to keep the control on third parties to deal with as the production limit tends to a good capital work frames.
Per Piece Production
- Co-packers generally don’t work on per piece production as its related to basic matters which tend to be a solitude deal to concern about.
- On part they work on the average consumption of single units of concern to feel for the rate of amount paid on scale.
- In general the packaging ,labour and tentative average costing are considered for mass production
Product Costing can be defined under the following flow chart
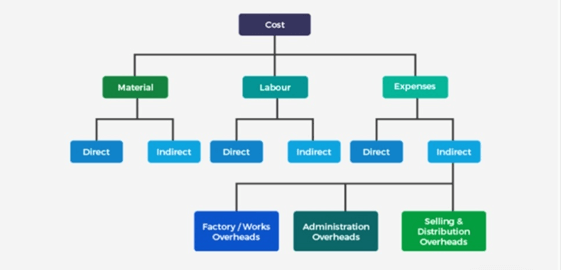
“Costing modules are set in accordance to the various needs of the organizational aspects like labour, expenses,material etc. ”
The main Product costing methods are:
- Job costing: This is the assignment of costs to a specific manufacturing job.
- Process costing: This is the accumulation of labour, material and overhead costs across departments or entities, with the total production cost then being allocated to individual units.
Aspects of Costing
- Job Costing : Job Costing (variable costing) considers the materials, labor and overhead costs and maps them to a production process to determine the cost.
- Standard Costing : This is one of the most common costing methodologies employed by manufacturing operations. Here the organization establishes ‘standard’ rates for materials and labor that are used in production or inventory
- Direct Costing: Is a costing methodology that only looks at variable costs (i.e. costs that increase or decrease proportionally with product output).
- Target Costing : Target costing takes a different approach to costing for unlike other methods this attempts to predict future costs and how those costs impact product pricing and desired profit margins.
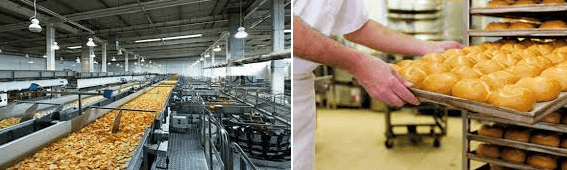
Adequate machineries and proper set up is the main concern of costing which can be saved if we opt for a good co-packer. Additional benefits of positioning ,packaging versatility according to market needs is added benefits.
Actual + % ( preferred by MNC):
Its on part of the organizations that the costing criteria to be dependent on
The actual costing (FG production to dispatch )including to the percentage of margin set by various parties on basis of average production.
Minimum Order Quantity
It’s a very important factor on which the co-manufacturers focus on as to get bulk orders in which they can work out with wholesale raw material rates, financial strategies, cut ups cost effectiveness and continuous flow of business. MOQ’S are set by suppliers to cover their cost of production and ensure that they make a profit off of each production run.